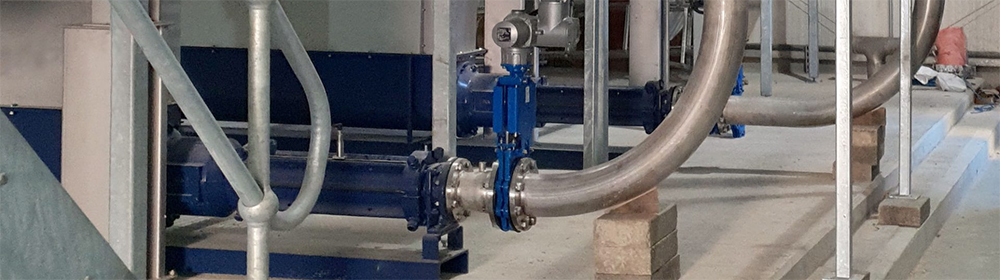
The modernisation project for a Sludge Treatment Facility involved the upgrade from a very energy intensive thermal drying plant to advanced anaerobic digestion using a thermal hydrolysis process. The scope of supply also included a new dewatering plant with three belt presses and three sludge cake pumps to transfer the dewatered sludge into the THP feed silos.
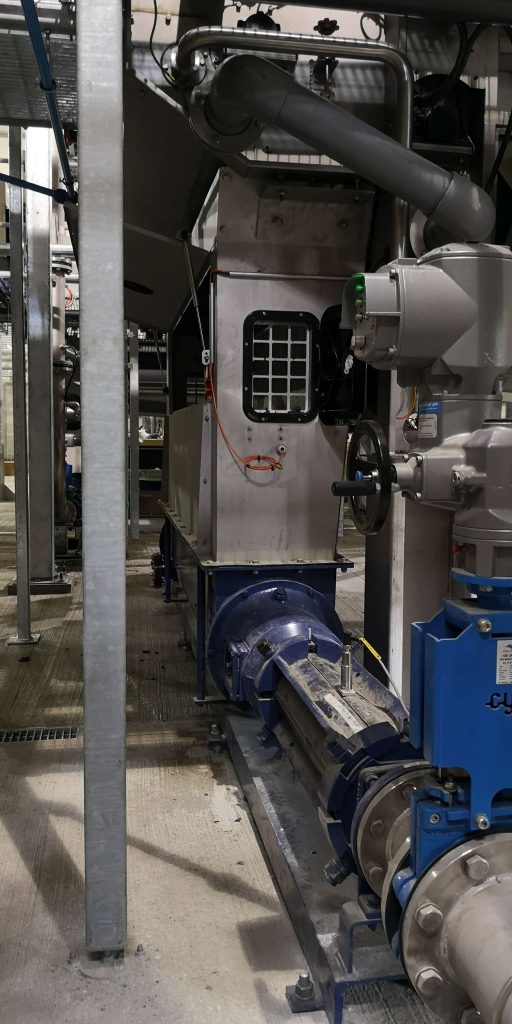 |
SEEPEX open hopper pumps sit under the belt presses
|
Compact, energy-efficient and flexible system for complex process
The upgrade project presented an immediate challenge: how to fit the new thermal hydrolysis process and dewatering plant into the restricted space of the existing building. The compact design of Veolia’s Exelys™ process significantly reduced the installation space required for the thermal hydrolysis process.
However, due to the space restraints, using a conventional multi-stage pumping system required to transfer 18-27% DS sludge cake through a total of 50m including vertical pipework with long-radius 90° bends would not be possible.
The dewatered sludge handling system needed to have the operational flexibility to accommodate a fully automated 24/7 operation with one, two or all three presses in operation at the same time, discharging into either of the two existing sludge cake silos through common discharge pipework.
Low energy and low discharge pressure solution for sludge cake transfer
With SEEPEX, the team explored how to install a sludge cake handling system within the reduced footprint. Upon consultation, SEEPEX’s Smart Air Injection (SAI) was selected: a highly efficient system involving a progressive cavity pump and pneumatic dense phase conveying technology, able to transport 16-40% DS dewatered sludge with a significantly lower operating pressure requirement.
SEEPEX supplied and commissioned three sludge cake pumps with 2.5m custom-made hoppers to suit the dimensions of the dewatered belt presses, the associated BLI pumps as well as the Smart Air Injection (SAI) controls.
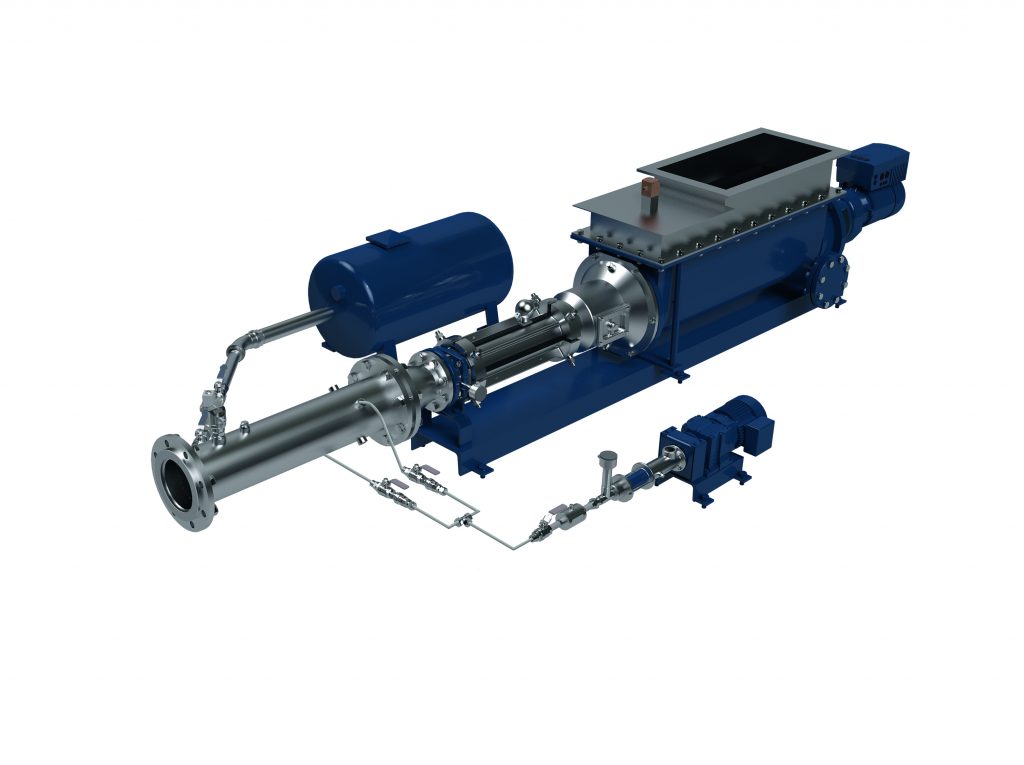 |
SAI technology is an energy efficient solution for long distance pumping, proven to significantly reduce operational and total investment costs.
|
The compact SAI system offered considerable savings by allowing the new plant to be installed within the existing sludge dryer building. By using dense phase conveying, they were able to lower the discharge pressure from 16-18 bar to 3-4 bar, enabling smaller cake pumps compared to the 4-stage pumps otherwise required for a conventional system.
The robust SAI system requires nearly 50% lower power compared to conventional pumping with subsequent energy cost savings. SAI has proven to have the operational flexibility required by the process and enables the pipework to be emptied when idle, eliminating the risk of cake line blockages; it is easy to operate and extremely reliable.
SEEPEX’s engineered solution using SAI technology and proven sludge cake pumping expertise enabled the team to upgrade their sludge cake handling system which feeds their thermal hydrolysis process at the Sludge Treatment Facility.