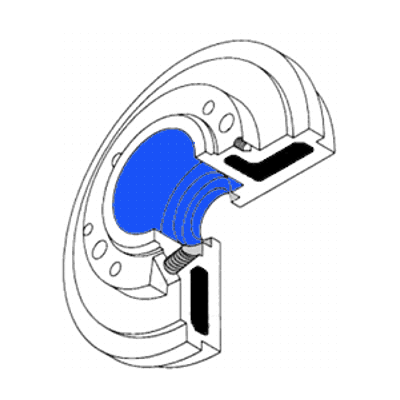
One of the most significant design changes introduced to the pump business in the last 30+ years is undoubtedly the large bore seal chamber. Introduced to the market place as part of the System One Pump from A. W. Chesterton, the concept was quickly snapped up by knowledgeable end users as a significant boost to mechanical seal life.
This was achieved by providing two significant benefits to the operation, longevity and reliability of the mechanical seal.
1. The increased volume of pumpage in the chamber permits the liquid to dissipate the heat generated by the seal faces much more readily than the lesser volume in a stuffing box. Consequently the mechanical seal will run cooler.
2. As the bore of the chamber is moved to a greater distance from the seal, the condition known as seal rub has been eliminated. (Seal rub is a condition where excessive radial shaft movement brings the seal into contact with the bore of the stuffing box, causing premature failure.)
A number of different seal chamber designs are currently in use.
The large cylindrical bore chamber is the same design as the stuffing box, except that the bore diameter is larger, but only in the area occupied by the seal. As the traditional close clearance is maintained at the bottom of the chamber, this perpetuates the capability to control the temperature and pressure of the pumpage inside the seal chamber.
The through bore design is also well used and, while it permits self draining and self venting of the seal chamber, it severely limits the amount of control that can be exerted on the pumpage in that area.
These design options are now widely available in almost every process pump in the market. More importantly, many companies have the option available to retrofit these seal chambers to older pumps which are still in use and can thus improve equipment reliability. If you haven't yet tried them out in your plant, they're worthy of careful consideration.
Ross Mackay is an internationally renowned expert in pumping reliability based in Canada. He specializes in helping companies increase their pump asset reliability and reduce operating and maintenance costs through pump training programs. He is the author of “The Practical Pumping Handbook”, and “The Mackay Self-Directed Pump Reliability Training System”. For more information and to register to possibly attend a Dynapumps and Ross Mackay pump school in 2013 please click here.